失效分析定义
对装备及其构件在使用过程中发生各种形式失效现象的特征及规律进行分析研究,从中找出产生失效的主要原因及防止失效的措施,称为失效分析。金属材料的失效形式及失效原因密切相关,失效形式是材料失效过程的表观特征,可以通过适当的方式进行观察。而失效原因是导致构件失效的物理化学机制,需要通过失效过程调研研究及对失效件的宏观、微观分析来诊断和论证。
失效分类
弹性变形失效:当应力或温度弓|起材料可恢复的弹性变形大到足以影响装备正常发挥预定的功能时,就出现弹性变形失效。塑性变形失效:当受载荷的材料产生不可恢复的塑性变形大到足以影响装备正常发挥预定的功能时,就出现塑性变形失效。
韧性断裂失效:材料在断裂之前产生显著的宏观塑性变形的断裂称为韧性断裂失效。
脆性断裂失效:材料在断裂之前没有发生或很少发生宏观可见的塑性变形的断裂称为脆性断裂失效。
疲劳断裂失效:材料在交变载荷作用下,经过一定的周期后所发生的断裂称为疲劳断裂失效。
腐蚀失效:腐蚀是材料表面与服役环境发生物理或化学的反应,使材料发生损坏或变质的现象,材料发生的腐蚀使其不能发挥正常的功能则称为腐蚀失效。腐蚀有多种形式,有均匀遍及材料表面的均匀腐蚀和只在局部地方出现的局部腐蚀,局部腐蚀又分为点腐蚀、晶间腐蚀、缝隙腐蚀、应力腐蚀开裂、腐蚀疲劳等。
磨损失效:当材料表现相互接触或材料表面与流体接触并作相对运动时,由于物理和化学的作用,材料表面的形状、尺寸或质量发生变化的过程,称为磨损。由磨损而导致构件功能丧失,称为磨损失效。磨损有多种形式,其中常见粘着磨损、磨料磨损、冲击磨损、微动磨损、腐蚀磨损、疲劳磨损等。
失效原因分析
设计不合理
其中结构或形状不合理,,材料存在缺口、小圆弧转角、不同形状过渡区等高应力区,未能恰当设计引起的失效比较常见。总之,设计中的过载荷、应力集中、结构选择不当安全系数过小追求轻巧和高速度)及配合不合适等都会导致构件及装备失效。构件及装备的设计要有足够的强度、刚度、稳定性,结构设计要合理。
分析设计原因引起的失效尤其要注意:对复杂构件未作可靠的应力计算;或对构件在服役中所承受的非正常工作载荷的类型及大小未作考虑;甚至于对工作载荷确定和应分析准确的构件来说,如果只考虑拉伸强度和屈服强度数据的静载荷能力,而忽视了脆性断裂、低循环疲劳、应力腐蚀及腐蚀疲劳等机理可能弓|起的失效,都会在设计上造成严重的错误。
选材不当及材料缺陷
金属装备及构件的材料选择要遵循使用性原则、加工工艺性能原则及经济性原则,首先要考虑遵循使用性原则。使在特定环境中的构件,对可预见的失效形式要为其选择足够的抵抗失效的能力。如对韧性材料可能产生的屈服变形或断裂,应该选择足够的拉伸强度和屈服强度;但对可能产生的脆性断裂、疲劳及应力腐蚀开裂的环境条件,高强度的材料往往适得反。在符合使用性能的原则下选取的结构材料,对构件的成形要有好的加工工艺性能。在保证构件使用性能、加工工艺性能要求的前题下,经济性也是必须考虑。
制造工艺不合理
金属装备及其构件往往要经过机加工(车、铣、刨、磨、钻等)、热冷变形(冲、压、卷、等)、焊接、装配等制造工艺过程。若工艺规范制订不合理,则金属设备或构件在这些加工成形过程中,往往会留下各种各样的缺陷。如机加工常出现的圆角过小、倒角尖锐、裂纹、划痕;冷热成形的表面凹凸不平、不直度不圆度和裂纹;在焊接时可能产生的焊缝表面缺陷(咬边、焊缝凹陷、焊缝过高)、焊接裂纹、焊缝内部缺陷(未焊透、气孔、夹渣), 焊接的热影响区更因在焊接过程经受的温度不同,使其发生组织转变不同,有可能产生组织脆化和裂纹等缺陷;组装的错位、不同心度、不对中及强行组装留下较大的内应力等。所有这些缺陷如超过限度则会导致构件以及装备早期失效。
使用操作不当和维修不当
使用操作不当时金属装备失效的重要原因之一 ,如违章操作,超载、超温、超速;缺乏经验、判断错误;无知和训练不够;主观臆测、责任心不强、粗心大意等都是不安全的行为。某时期统计260次压力容器和锅炉事故中,操作事故194次,占74.5%。装备是要进行定期维修和保养的,如对装备的检查、检修和更换不及时或没有采取适当的修理、防护措施,也会弓|起装备早期失效。
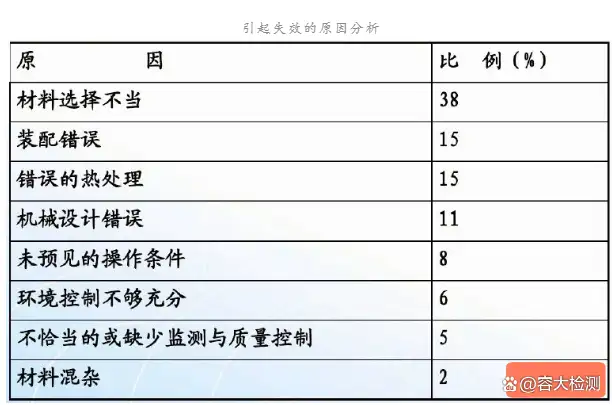
引起失效的常见缺陷
铸态金属组织缺陷
铸态金属常见的组织缺陷有缩孔、疏松、偏忻、内裂纹、气泡和白点等。
缩孔
金属在冷凝过程中由于体积的收缩而在铸锭或铸件心部形成管状(或喇叭状)或分散的孔洞,称为缩孔。缩孔的相对体积与与液态金属的温度、冷却条件以及铸件的大小等有关。液态金属的温度越高,则液体与固体之间的体积差越大,而缩孔的体积也越大。向薄壁铸型中浇注金属时,型壁越薄、则受热越快, 液态金属越不易冷却,在刚浇完铸型时,液态金属的体积也越大,金属冷凝后的缩孔也就越大。
疏松
在急速冷却的条件下浇注金属,可避免在铸锭 上部形成集中缩孔,但此时液体金属与固态金属之间的体积差仍保持-定的数值, 虽然在表面上似乎已经消除了大的缩孔,可是有许多细小缩孔即疏松,分布在金属的整个体积中。钢材在锻造和轧制过程中,疏松情况可得到很大程度的改善,但若由于原钢锭的疏松较为严重、压缩比不足等原因,则在热加工后较严重的疏松仍会存在。此外,当原钢锭中存在着较多的气泡,而在热轧过程中焊合不良,或沸腾钢中的气泡分布不良,以致影响焊合,亦可能形成疏松。
疏松的存在具有较大的危害性,主要有以下几种: (1) 在铸件中,由于疏松的存在,显著降低其期学性能,可能使其在使用过程中成为疲劳源而发生断裂。在用作液体容器或管道的铸件中,有时会存在基本.上相互连接的疏松,以致不能通过水压试验,或在使用过程中发生渗漏现象; (2) 钢材中如存在疏松,亦会降低期学性能,但因在热加工过程中一般能减少或消除疏松,故疏松对钢材性能的影响比铸件的小; (3) 金属中存在较严重的疏松,对机械加I后的表面粗糙度有一定的影响。
偏析
金属在冷凝过程中,由于某些因素的影响而形成的化学成分不均匀现象称为偏析。偏析分为晶内偏析、晶间偏析、区域偏析、比重偏析。由于扩散不足,在凝固后的金属中,便存在晶体范围内的成分不均匀现象,即晶内偏析。基于同-原因,在固溶体金属中,后凝固的晶体与先凝固的晶体成分也会不同,即晶间偏析。碳化物偏析是-种晶间偏析。
在浇注铸键(或铸件)时,于通过铸型壁强烈的定向散热,在进行着凝固的合金内便形成一个较大的温差。结果就必然导致外层区域富集高熔点组元,而心部则富集低熔点组元,同时也富集着凝固时析出的非金属杂质和气体等。这种偏析称为区域偏析。在金属冷凝过程中,如果析出的晶体与余下的溶液两者密度不同时,这些晶体便倾向于在溶液中下沉或上浮,所形成的化学成分不均匀现象,称为比重偏析。晶体与余下的溶液之间的密度差越大,比重偏析越大。这种密度差取决于金属组元的密度差,以及晶体与溶液之间的成分差。如果冷却越缓慢,随着温度降低初生晶体数量的增加越缓慢,则晶体在溶液中能自由浮沉的温度范围越大,因而比重偏析也越强烈。
气泡
金属在熔融状态时能溶解大量的气体,在冷凝过程中因溶解度随温度的降低而急剧减小,致使气体从液态金属中释放出来。若此时金属已完全凝固,则剩下的气体不易逸出,有一部分就包容在还处于塑性状态的金属中,于是形成气孔,则称其为气泡。气泡的有害影响表现如下: (1) 气泡减少金属铸件的有效截面,于其缺口效应,大大降低了材料的强度; (2) 当铸锭表面存在着气泡时,在热锻加热:时可能被氧化,在随后的锻压过程中不能焊合而形成细纹或裂缝; (3) 在沸腾钢及某些合金中,于气泡的存在还可能产生偏析导致裂缝。
白点
在经侵蚀后的横向截面上,呈现较多短小的不连续的发丝状裂缝;而在纵向断面上会发现表面光滑、银白色的圆形或椭圆形的斑点,这种缺陷称为白点。白点最容易产生在镍、铬、锰作为合金元素的合金结构钢及低合金工具钢中。奥氏体钢及莱氏体钢中,从未发现过白点;铸钢中也可能发现白点,但极为罕见;焊接工件的熔焊金属中偶尔也会产生白点。白点的产生与钢材的尺寸也有-定的关系,横截面的直径或厚度小于30mm的钢材不易产生白点。通常具有白点的钢材纵向抗拉强度与弹性极限降低并不多,但伸长率则显著降低,尤其是断面收缩率与冲击韧性降低得更多,有时可能接近于零。且这种钢材的横向力学性能比纵向力学性能降低得多。因此具有白点的钢材一般不能使用。