某石化公司的压力容器进行全面检验时,发现投用的液态烃沉降罐(材质16MnR)罐体内壁表面有氢致鼓包多处,其最大直径约200 mm。另外在换热器、异构化装置、液化石油气储罐及富气水洗罐中也发现了鼓包、微裂纹及分层现象。其中一些设备存在的缺陷在原工艺条件下会继续产生和扩展。由于这些缺陷类似且较多,因此对其进行分析研究,提出相应的措施对存在缺陷设备的安全运行有重要意义。
原因分析
该公司所用原油中含硫量有时偏高,从设备使用单位的分析数据得知,已出现问题设备的介质中不同程度都含有硫。原油在提炼中虽经脱硫处理但脱硫效果并不稳定,因此,湿硫化氢环境(H2S+H:0型的腐蚀环境)广泛存在于炼油厂原油加工的第一道工序、炼油厂二次加工装置的轻油部位、石油化工催化装置及液化石油气储罐等部位。
根据有关文献并结合该石化分公司的实际情况,设备介质中存在硫化氢成分是导致上述压力容器发生腐蚀损坏的根本原因。
另外,在使用中也存在着许多引起局部高应力的因素,包括力学或化学损伤,诸如磨损、磨蚀、点蚀、晶间腐蚀、浓差电池腐蚀、缝隙腐蚀等各种形式的局部腐蚀;构件各部分处于不同温度下产生的温差应力;碳、氢、氮、氧等气态碳化物介质扩散进入金属构件内部及存在残余应力等。当应力和腐蚀环境组合时,很容易造成设备的腐蚀与损坏。
腐蚀机理
在湿的硫化氢环境中,氢致破坏是因为产生原子氢而引起的。原子氢是腐蚀反应的副产物,之后,原子氢会扩散进入钢中。如下所示,钢与含水硫化氢发生腐蚀反应时,就会产生原子氢(H)和分子氢(H2):
Fe + H2S → FeS + 2 H ,接着,2H → H2
碳钢设备发生均匀腐蚀和湿硫化氢应力腐蚀开裂。开裂的形式包括以下几种。
(1)氢鼓泡含硫化合物腐蚀过程析出的氢原子向钢中渗透,在裂纹、夹渣、缺陷等处聚集并形成分子,从而形成很大的膨胀力。随着氢分子数量的增加,对晶格界面的压力不断增高,导致界面开裂形成氢鼓泡。主要分布在设备内壁的浅表面。
(2)氢致开裂在钢材内部发生氢鼓泡的区域,当氢的压力继续增高时,小的鼓泡裂纹趋向于相互连接,形成阶梯状特征的氢致开裂,分布在平行于表面方向,钢中MnS夹杂带状组织分布会增加氢致开裂的敏感性。
(3)硫化物应力腐蚀开裂湿硫化氢环境中产生的氢原子渗透到钢的内部,溶解于晶格中导致氢脆,在外加应力或残余应力作用下形成开裂。它通常发生在焊缝与热影响区等高硬度区。
(4)应力导向氢致开裂在应力引导下,在夹杂物与缺陷处因氢聚集而形成成排的小裂纹沿着垂直于应力的方向发展。它通常发生在焊接接头的热影响区及高应力集中区,如接管处、几何形状突变处、裂纹状缺陷处或应力腐蚀开裂处等。
湿硫化氢开裂是在湿硫化氢环境中发生的一种氢致破坏形式。在湿硫化氢环境中,因为存在氢而发生的其他破坏形式包括:
氢鼓泡
硫化物应力开裂(SSC)
氢致开裂(HIC)
应力定向氢致开裂 (SOHIC)
一、氢致开裂(HIC)及氢鼓泡
氢致开裂是平行的氢层连通在一起产生穿壁裂缝造成的,它们与外加应力或残余应力没有明显的相互作用。在鼓泡处,氢在内部聚积产生的应力加剧了氢致开裂。氢致开裂与钢材的净度密切相关,并且与钢的制造方法、存在的杂质和它们的形状有关。实验室执行标准GB/T8650-2015、NACE TM0284-2016
非均质的细长的硫化物或氧化物夹杂物如果是与钢板轧制方向平行发生的,一般都会发生氢致开裂。这些夹杂物构成形成显微氢鼓泡的场所,这些显微鼓泡会生长,并且最终通过台阶状裂缝连在一起。事实上,有时候把氢致开裂叫做台阶状开裂。
由于氢致开裂对应力没有依存关系,也不是伴随硬化的显微结构发生的,所以,焊后热处理一点作用也没有。限制硫这样的痕量元素以及控制钢的制造变量,才能使钢具有氢致开裂抗性。
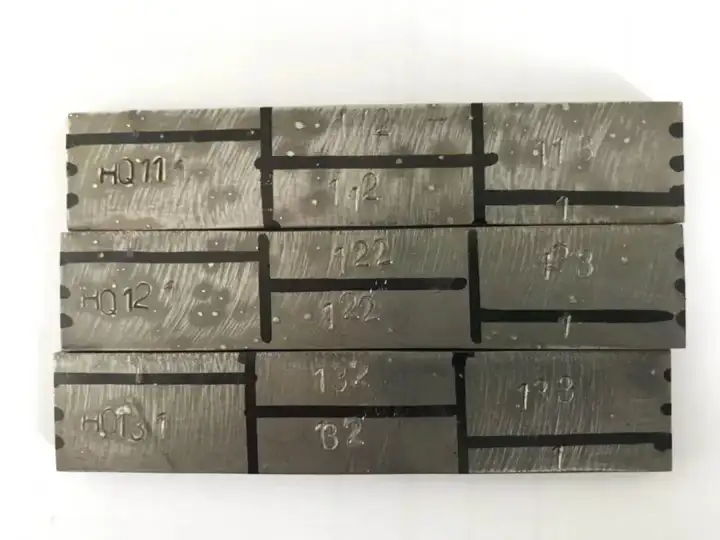
氢鼓泡图
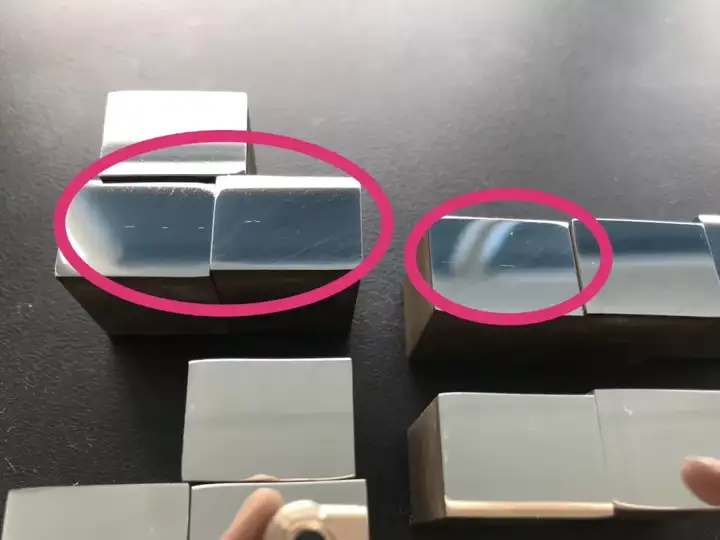
宏观下氢致裂纹图
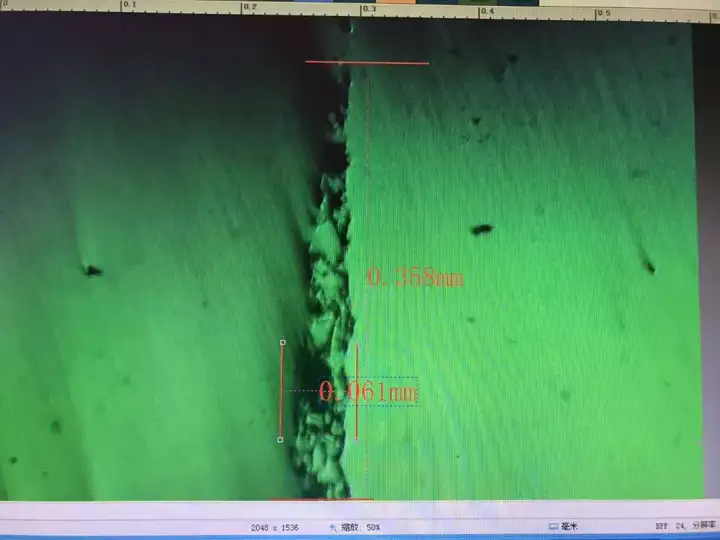
放大100x下观察裂纹图片
氢鼓泡是原子氢扩散进入钢材并在空隙、夹层或非金属夹杂物处被截获而造成的。正如上文已经提及的,进入这些部位的氢原子结合在一起会形成分子氢,而分子氢是无法向外扩散而逸出的。聚集在一起的氢气的膨胀压力终使部件发生穿壁分离,并在金属表面出现明显的鼓泡。
氢鼓泡会出现在一块板的两面,或者鼓泡出现在另一鼓泡顶上,取决于夹层的位置。它们大小不一,从小的突起到几英尺直径的肿胀。不断增大的鼓泡会使表面发生扯裂,使设备失去承压能力。
二、硫化物应力开裂(SSC)
硫化物应力开裂(SSC)是一种氢脆开裂形式,假如高强度钢、硬焊缝和焊接热影响区(HAZs)处于酸性环境中,受到拉伸应力作用,并且温度低于82°C(180°F),就会发生硫化物应力开裂。钢材的硫化物应力开裂易发性在很大程度上取决于其组成、显微结构、强度、残余应力、外加应力。
将施加应力的试样浸泡在含H2S的酸性水溶液环境中,通过施加合适增量的载荷获得材料抗SSCC性能数据。实验室执行标准GB/T 4157-2017 及NACE TM0177-2016
拉伸法
评价在单轴拉伸加载下的金属抗SSCC性能。通常用断裂时间确定SSCC敏感性。通过对拉伸试样施加特定应力级的载荷进行720h试验,给出断裂/未断裂或开裂/未开裂试验结果。
试样简单,应力状况明确,试验结果易于判定,能由断裂时间定量评定。但试验周期长(一般需进行720h试验),限制需进行此项试验的钢板、设备等生产厂家的生产进度。
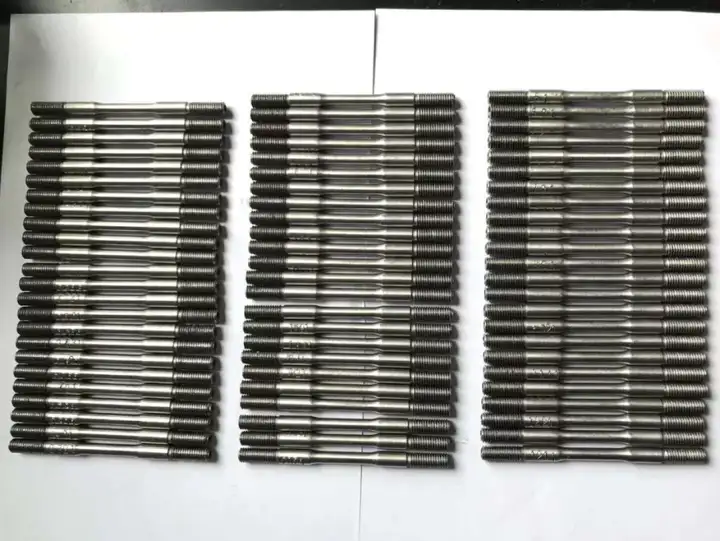
拉伸试样图
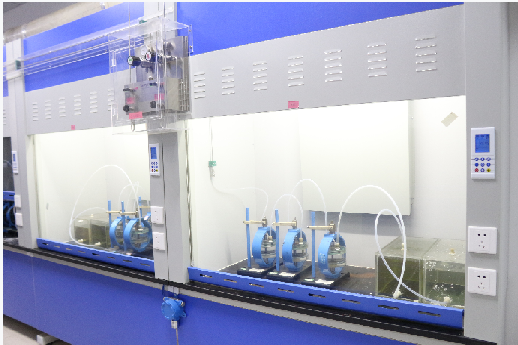
拉伸试验装置图
四点弯试验
评价材料存在应力集中时的SSCC敏感性。将弯梁试样加载到特定挠度,并将受力试样暴露在特定的试验环境中。试验结束后在低倍显微镜下观察受拉伸面,给出开裂破坏/未破坏的试验结果。
四点弯试样尺寸简单,便于试验小、局部和薄的材料。且加载装置精巧、经济、可靠、独特,使用方便。但试验周期较长,定量研究困难。
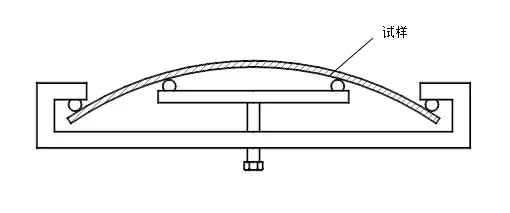
四点弯曲加载装置图
三、应力定向氢致开裂(SOHIC)
应力定向氢致开裂(SOHIC)与氢致开裂相似,所不同的是应力定向氢致开裂是受应力驱动的,并且开裂方向与基本应力方向是垂直的。在原先有其他裂缝或缺陷的焊接热影响区,常见应力定向氢致开裂。由于裂缝形成和发展过程中存在应力的影响,所以,为减小应力定向氢致开裂,焊后热处理多少是有点效用的。控制制造变量和痕量元素也是有效的。
四、其它腐蚀试验介绍
完整环试验
由英国出版的BS 8701-2016完整环试验的优点是不需要对管线管完整环试样加压以达到所需的应力载荷,并保留残余应力。同时,也可以使用机械方法通过椭圆化使管道变形来产生等效应力。其他优点则在于代表性试样和单面暴露。
此项试验使用经过反复验证的实验程序,在管钢的完整环状管段上的两个区域分别施加已知的应力水平。然后将管道试样内部暴露于酸性测试用溶液中,尽管有些情况下可能需要外部的酸性介质。在暴露期间定期开展超声波监测和氢气渗透测量。因此,可以监测起裂和裂纹扩展的过程。最后,还开展了适应症的金相学研究,以对超声波检测发现的任何缺陷进行分类。
慢应变速率应力腐蚀试验(SSRT)
使暴露到特定环境中的试样承受逐渐增加的应变,通过特征参数评定应力腐蚀开裂的敏感性。
1、试验标准NACE TM0198-2011 ASTM G129-2013 GBT 15970.7-2000(idt ISO 7539-7:1989)金属和合金的腐蚀 应力腐蚀试验 第7部分:慢应变速率试验
2、试验介质
涉及高温高压、混合气体各种腐蚀环境。
3、试验方法
分别在惰性环境和同一温度的腐蚀性环境中以相同的应变速率进行试验。试验后首先将在惰性介质中的各特征参数与在腐蚀介质中的特征参数(断面收缩率、最大载荷、内积功等)进行对比,得到应力腐蚀敏感性指数ISCC来评定应力腐蚀开裂敏感性。关于ISCC衡量应力腐蚀开裂敏感性大小的一般评定:当ISCC>35%,研究体系具有明显的应力腐蚀倾向;当ISCC介于25%~35%之间,研究体系有应力腐蚀倾向;当ISCC<25%,研究体系没有明显的应力腐蚀倾向。然后借助低倍显微镜进行二次裂纹的宏观观察。最后借助扫描电镜对试样断面进行断口形貌观察,确定有无应力腐蚀特征。
SSRT试验能够快速评价特定金属与环境组合的应力腐蚀开裂敏感性,试验参数易于控制。
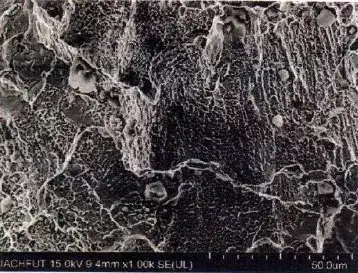
实验后的电镜扫描图
不锈钢在沸腾氯化镁溶液中应力腐蚀试验
评定不锈钢在沸腾氯化镁溶液中的应力腐蚀敏感性。试验标准YB/T 5362-2006 及ASTM G36-94 试验介质氯化镁溶液(加热调整其沸点为143℃±1℃或155℃±1℃)。试验方法
(1)恒负荷拉伸试验
将试样装在试验装置上,试验溶液加热至沸腾后注入试验容器并加热,待到再开始沸腾时立即加载。从加载到试样断裂的时间作为破断时间或根据协商确定试验时间及周期,试验结束后检查有无裂纹。
力学条件明确,能由破断时间定量评定试验结果。
(2)U型弯曲试验
试验溶液完全沸腾后,放入施加应力的试样。隔一定时间取出试样,用5~15倍放大镜观察试样的破裂情况。
U型弯曲试样尺寸简单,便于加载,适用于局部和薄的材料。但力学条件不明确,定量研究困难。
试验装置图
金属和合金的腐蚀不锈钢晶间腐蚀
《金属和合金的腐蚀 镍合金晶间腐蚀试验方法》 GB/T 15260-2016
《金属和合金的腐蚀 不锈钢晶间腐蚀试验方法》 GB/T 4334-2008
《不锈钢耐晶间腐蚀的测定。第1 部分:奥氏体和铁素奥氏体不锈钢-在硝酸介质中的质量损失的腐蚀试验 》 ISO 3651.1-1998
《不锈钢耐晶间腐蚀性的测定。第2 部分:铁素体,奥氏体和铁素-奥氏体不锈钢--在含硫酸的介质中的腐蚀试验》 ISO 3651.2-1998
《煅制高镍铬轴承合金晶间腐蚀敏感性的检查用标准试验方法》ASTM G28-02(2015)
《检测奥氏体不锈钢晶间腐蚀敏感度的标准方法》 ASTM A262-15
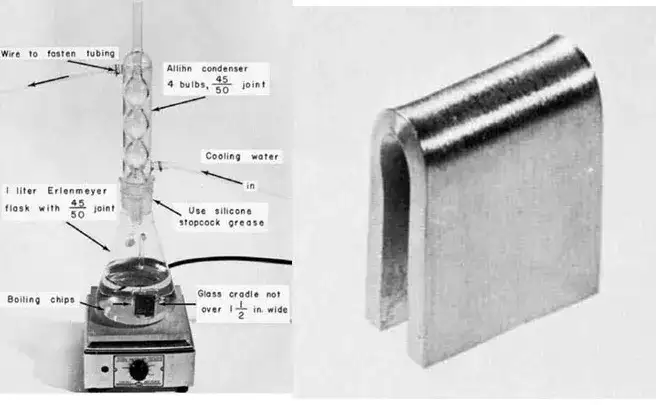
晶间腐蚀E法腐蚀后弯曲图
缝隙腐蚀
《不锈钢三氯化铁缝隙腐蚀试验方法》 GB/T 10127-2002
《金属及其合金在沸腾氯化镁溶液中应力腐蚀开裂性能》 ASTM G36-94(2018)
铁-铬-镍合金高温水中应力腐蚀试验
《铁-铬-镍合金在高温水中应力腐蚀试验方法》 YB/T 5344-2006
金属均匀腐蚀全浸试验
《金属材料实验室均匀腐蚀全浸试验方法》 JB/T 7901-1999
腐蚀点蚀评定
《用氯化铁溶液测定不锈钢和相关合金点状腐蚀和隙间腐蚀的试验方法》 ASTM G48-11 (2015)
《金属和合金的腐蚀 点蚀评定方法》 GB/T 18590-2001
《金属和合金的腐蚀 不锈钢三氯化铁点腐蚀试验方法》 GB/T 17897-2016
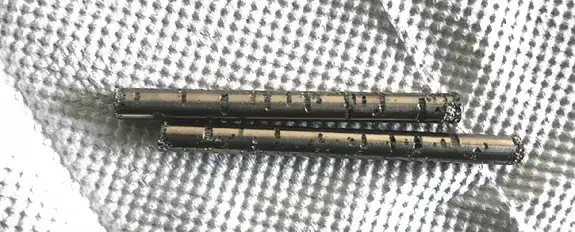
缝隙腐蚀图
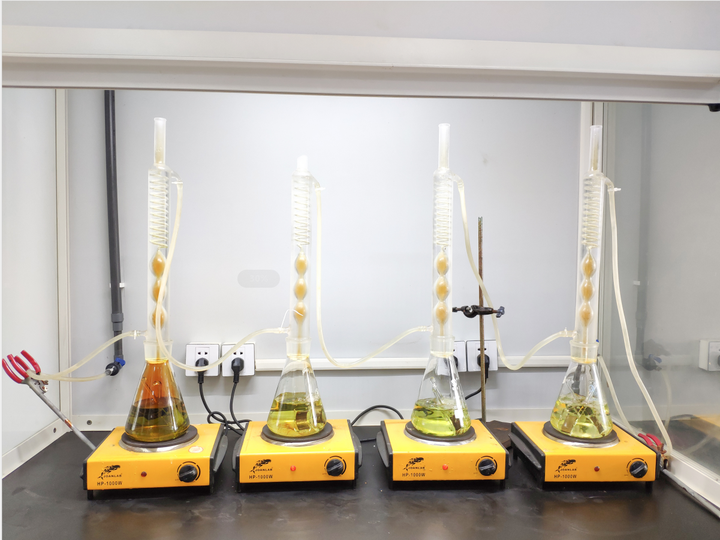
涉及测试:
硫化物应力开裂(SSC)
氢致开裂试验(HIC试验)
应力导向氢致开裂试验(SOHIC)